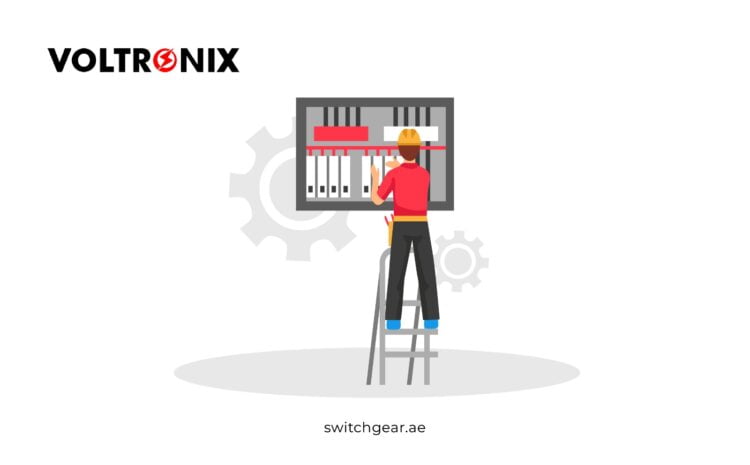
Electrical Control Panel Troubleshooting: Tips and Techniques for DOL Starter, Star Delta, and Soft +Starter Rectification
Many industrial and commercial applications demand electrical control panels because they manage and secure electrical systems and equipment. However, with time, these control panels may develop problems and malfunctions, slowing operations and possibly posing a safety risk. The electrical control panel troubleshooting entails locating and fixing these issues to restore proper functionality. Electrical control panel troubleshooting calls for a systematic approach, adherence to safety procedures, and a thorough comprehension of the control panel’s parts and how they work.
Identifying the problem’s underlying source involves looking at various components, including the power supply, wiring parts, and control circuits. There are several effective troubleshooting procedures that include essential elements, including visual examination, power supply verification, connection verification, control security assessment, component testing, and adherence to pertinent documentation and guidelines.
Across-the-line starter, also known as DOL starter (Direct Online Starter). A DOL starter is a tool that starts motors with a main contactor, safety features, and an overload relay. It is used for low-rating motors, often those with less than 5 HP.
Electrical Control Panel Troubleshooting: Tips and Techniques for DOL Starter
Confirm voltage supply- Confirming the power supply is essential in troubleshooting electrical control panels. This requires verifying that the power source is providing adequate voltage and current as well as that the electrical input to the control panel is within the allotted ranges. This process helps identify potential power quality problems, such as voltage variations or insufficient power supply.
- Examine Motor Contactor- The contactor is crucial to the DOL starter. When evaluating the contactor, check for any signs of damage, overheating, or burned contacts. If it is required to clean or replace the contactor, proceed.
- Assess current relay- The overload relay guards the motor against excessive current flow. To ensure that the overload relay is working correctly, test it. Adjust the overload setting if necessary.
- Motor connections- Look for damaged or loose wires at the motor connections. Make that the contractor’s motor terminals are properly fastened and tightened.
- Validate control circuit- Analyze the DOL starter’s control circuitry. Inspect the auxiliary contactors, push buttons, and control wires for any loose connections or other issues.
- Troubleshoot initial operation- Consider potential problems, including an insufficient power supply, a broken contactor, improper motor connections, or motor overload if the motor won’t start or behaves oddly. Eliminate each option one by one to identify the underlying issue.
- Examine control panel units- Visually examine all the control panel’s parts, including the fuses, circuit breakers, relays, and terminal connections. Restore any broken or defective parts or fuses.
Star Delta Starters are frequently used in electrical installations to control the motor’s beginning current while starting large-rating squirrel cage induction motors. Needs to be known by every engineer and electrician regarding the potential issues that could arise with the starter or motor that is connected to them. Let us see the problems that could occur associated with Star Delta Starters.
- Motor starts with strong current demand and trips.
- The motor does not arrive in the Delta and continues to operate in the Star.
- The transition from Star to Delta blows the fuses.
- During the transition from start to Delta, a motor overcurrent excursion looks for motor current.
Factors to be checked for troubleshooting for Star Delta Starters
- Motor starts with strong current demand and trips.
When a motor starts with a high current draw and trips later, it may be a sign of a problem with the motor’s starting system or a more severe issue with the motor itself. Inrush current, which rises because of the initial surge of power required to overcome the motor’s inertia and start rotating, is the term for this high current demand during motor startup. Mechanical overload, voltage imbalance, insufficient motor starting torque, and motor winding problems are some causes of this problem. To stop future damage to the motor or electrical system. It is imperative to look into and solve the core cause of the issue.
- The motor does not arrive in the Delta and continues to operate in the Star.
A potential problem with the motor’s switching mechanism or control circuit is indicated when a motor continues to run in the star configuration rather than switching to the data configuration. It may be required to thoroughly inspect and troubleshoot these parts to discover and fix any problems that prevent the contactors, timers, or wiring connections from switching from Star to delta mode.
- The transition from Star to Delta blows the fuses.
Suppose the switchover from Star to delta arrangement blows the fuses. In that case, it can be caused by an overload or short circuit, damaged wiring, faulty or improperly wired contractors or a mismatch in the motor phases could be blamed for this problem.
- During the transition from start to Delta, a motor overcurrent excursion looks for motor current.
It is essential to set the timer’s time accurately. The motor’s current drops as it accelerates in a star-shaped pattern. However, it is only feasible if the load on the motor is smaller than its capacity to provide torque. However, it is only practical if the load on the motor is less than its ability to generate torque. This guarantees that the motor may accelerate smoothly in a star-shaped pattern, and to accomplish this, the timer’s time setting needs to be precise.
Electrical Control Panel Troubleshooting+Soft +Starter Rectification
- When debugging, a short-phase failure happens, and the soft starter’s trouble light illuminates while the motor is inactive. It’s advisable to investigate and correct the electrical issue immediately, inspect the right connections, and seek more advice from the soft starter’s manual or technical support.
- When the soft starter kicks on but the bypass contactor doesn’t engage-The smaller settings cause the protection device to malfunction during the starting phase. Setting the soft starter’s parameter is ridiculous ( It resets the soft starter’s characteristics and is mainly intended for soft starters under 55kw)
- Occasionally during the initial phase, an air switch trips. – The air switch’s delay setting is too short or doesn’t fit the motor (expand the air switch’s specifications or select the appropriate air switch). Large grid voltage variations throughout the starting process would cause the soft starter to issue incorrect instructions, resulting in the advance bypass.
- The display panel is blank or shows jumbled codes. The soft starter doesn’t function when the user utilizes it.- When the soft starter is running, the internal connection wire becomes loose owing to the vibration of the external elements (open the soft starter’s external cover and firmly connect the display screens wires.)
- When a soft starter fails to function, it provides a failure warning, and the motor does not operate.- Phase where there is no motor ( verify peripheral circuits and motor). Check to see if the motor and grid voltage are out of the ordinary—Silicon control of the main component in the soft starter shorts.
- When a load is started by a soft starter over time, the soft starter eventually ceases, and the motor pulls up freely.- Incorrect parameter setup ( parameter reset, minor increase in beginning voltage and time).
In Conclusion, It can be challenging to diagnose electrical control panel, especially when working with DOL starters, star delta layouts, and soft starters. However, businesses can offer important support in resolving problems with these control panel components if they have the correct methods and knowledge. Companies can ensure the smooth and reliable running of their electrical systems, reducing downtime and increasing productivity by enlisting the assistance of renowned organizations like Switchgear specializing in these fields.